DRIVEN BY 3D PRINTING
Ready to improve vehicle design and engineering
COMPILED BY Dyan Seneviratne
Stand by for a mind-boggling game changer: revolutionary 3D printing is set to radically change how cars are designed – and indeed, engineered! It is being called a manufacturing process that’s ‘revolutionary.’
Like the legendary pioneer Henry Ford’s 1913 Model T production line, 3D printing can turn a whole industry on its head. And those who fail to see the looming revolution will inevitably fall by the wayside!
So what is 3D printing?
3D printing or additive manufacturing is a process that goes straight from computer aided design to finished items with no waste. There’s none of the heaps of discarded material that traditional machining, casting or moulding produce.
Significantly, materials are built up layer upon layer with 3D printing in only the areas and specific quantities required. It also opens the door for complex biochemical structures – ingenious engineering inspired by nature, which adds strength only where needed!
And what’s so clever about 3D printing for cars?
According to Gordon Murray Design’s Director of Research and Development Andy Smith, “you can try things with it that you can’t do with conventional mouldings – for instance, there’s no need to worry about die draws and draft angles – so you can do whatever you want within reason.”
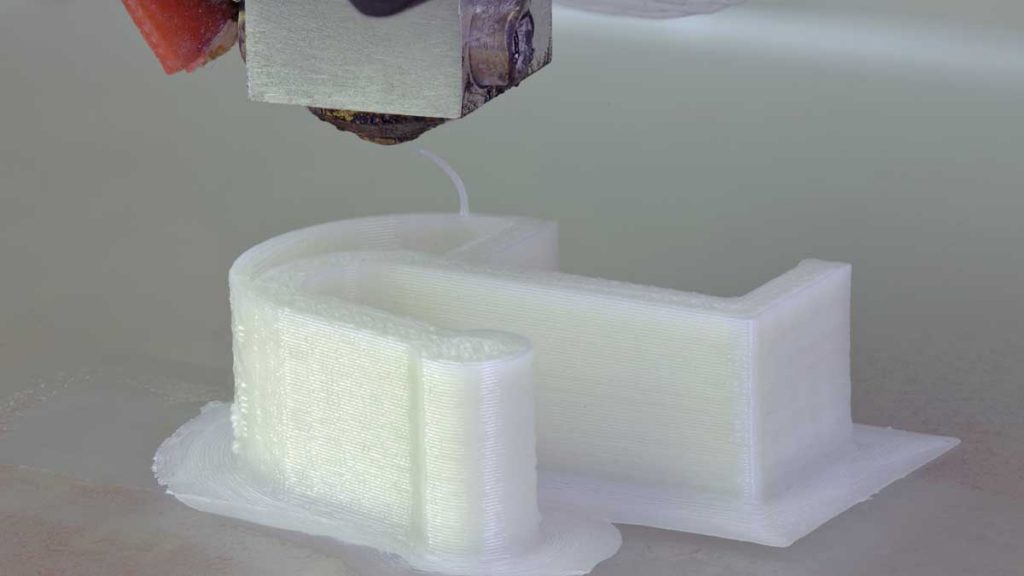
“Titanium is a good example. It’s not cheap but you can use it very effectively in the right places, saving on weight and costs,” Smith asserts. Weight saving translates into greater efficiency with weight to power ratios enhanced and overall mobility improved.
Former Jaguar design chief Ian Callum now runs his own design and engineering business. He explains: “The biggest advantage for me is getting to the final design of a component with mechanical or aesthetic very quickly from a prototype. I am not a great fan of assessing a product only on CAD – you can build prototypes from them and still have issues.”
“For us, it also means we can produce one-off items for customers, or do limited production runs without huge investments or castings that aren’t financially viable,” Callum elaborates.
Meanwhile, Director of Automotive Business and 3D specialist at Stratasys Fadi Abro reveals that “Ford and GM are investing heavily in 3D printers that are a part of the manufacturing process – a production application but not a production part. These printers can produce manufacturing tools that are lighter, 90 percent cheaper, and free of design restrictions that conventional machining and casting places on engineers.”
“The past decade has been about material development. But the next five to 10 years will be all about ramping up production speeds to be competitive with traditional technology. By then, OEMs (Original Equipment Manufacturers) will be thinking of 3D printing first rather than today’s traditional manufacturing techniques,” he adds.
Abro elaborates: “It will enable biomimicry – think about a spider’s web, which is created in a minimalist way to support its activity. Organic designs combined with lightweight polymers will deliver big weight savings for electric vehicles, pickups and large SUVs.” So it seems the future is laced with breathtaking developments made possible by 3D printing!